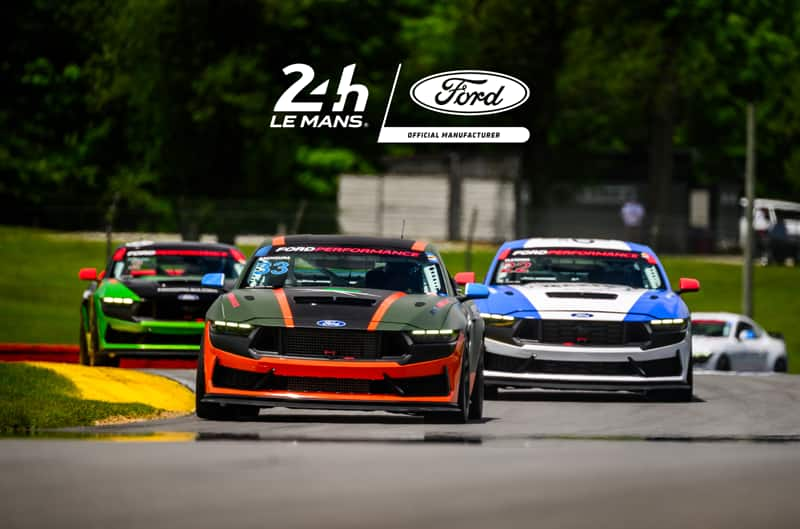
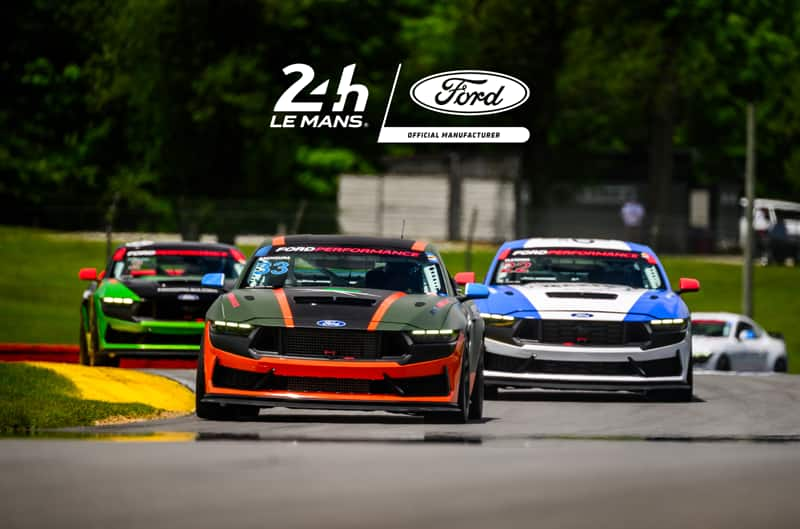
All News
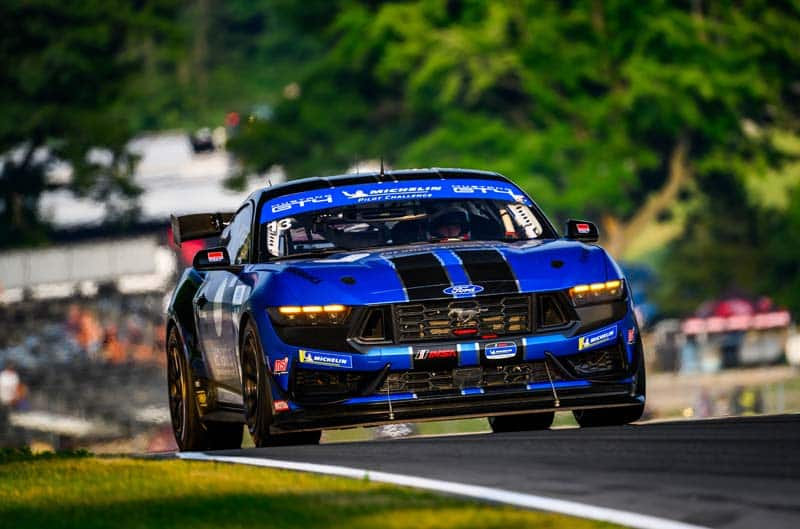
Ford Performance Weekend Highlights | August 3, 2025
By Ford Performance Staff
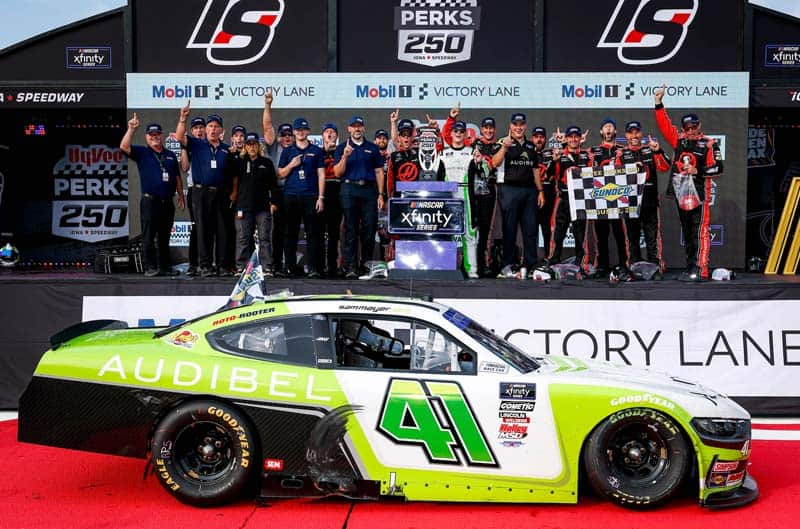
Sam Mayer Scores NASCAR Xfinity Series Win at Iowa
By Ford Performance Staff
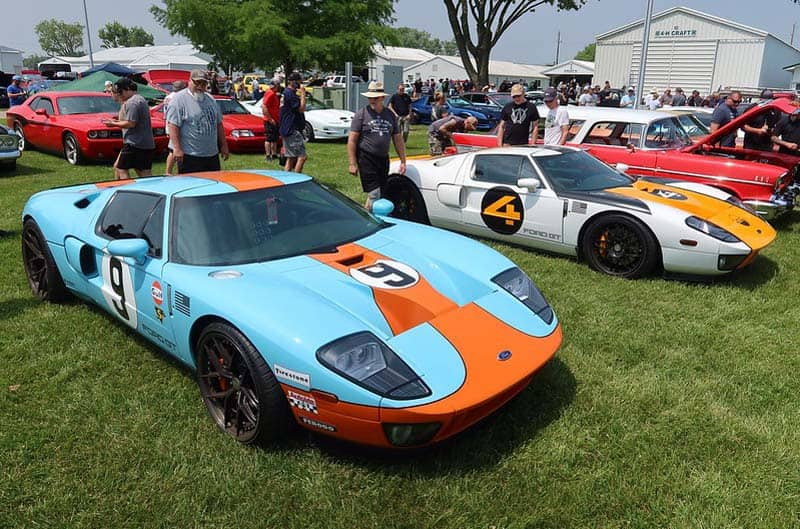
Ford Rides Rev Up Hot Rod Power Tour Stop in Michigan
By Bill Cook

T-Birds Headline Aug. 14 Homecoming Event in Dearborn
By John M. Clor
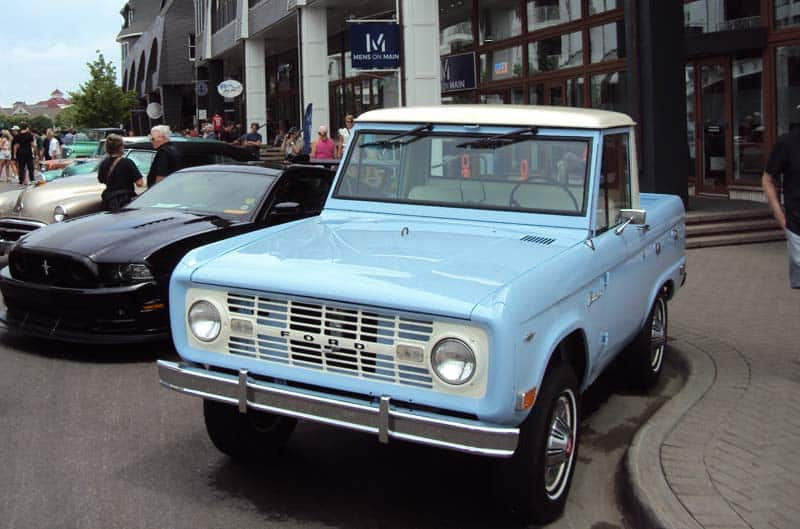
Mustangs Make Waves at Bay Harbor Car & Boat Show
By John M. Clor
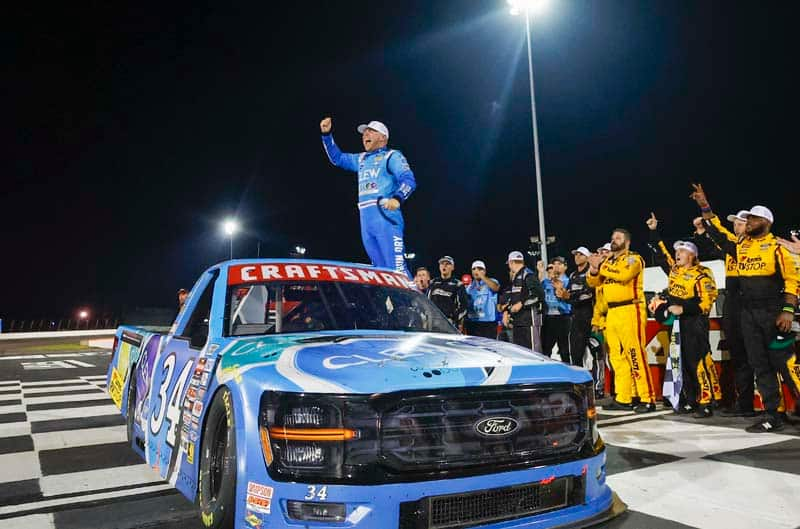
Ford Performance Weekend Highlights | July 27, 2025
By Ford Performance Staff
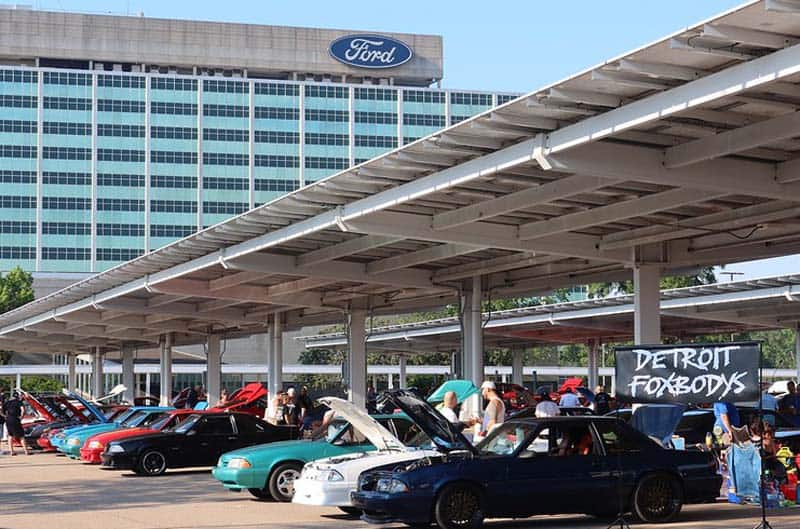
MotorCity FoxFest Storms Ford’s WHQ for 3rd Annual Show
By MCFF Team & Bill Cook
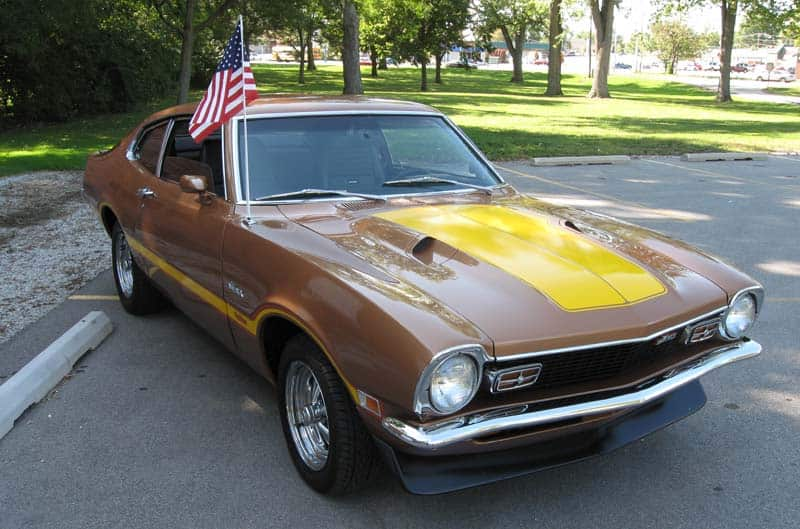
Tom Lehman’s Resto Turns ’72 Maverick from Rust to a Ge
By Tom Lehman
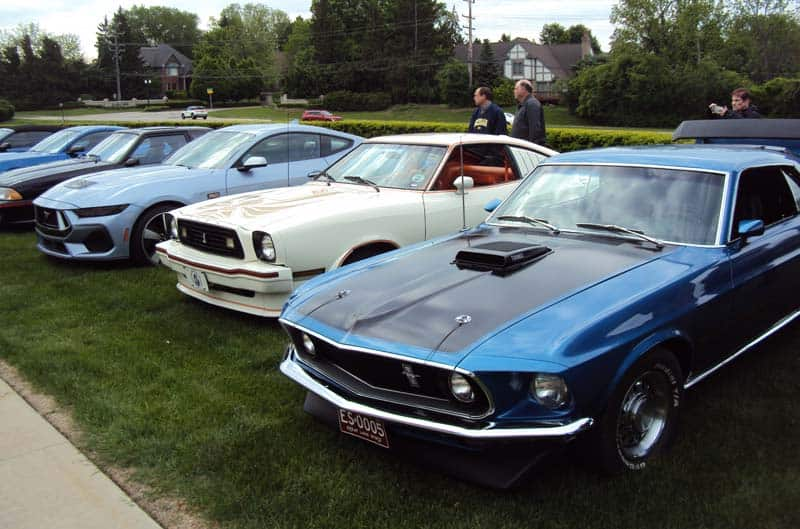
Mustangs Deliver Fitting Tribute at Sperlich Memorial
By John M. Clor

Ford Performance Weekend Highlights | July 20, 2025
By Ford Performance Staff
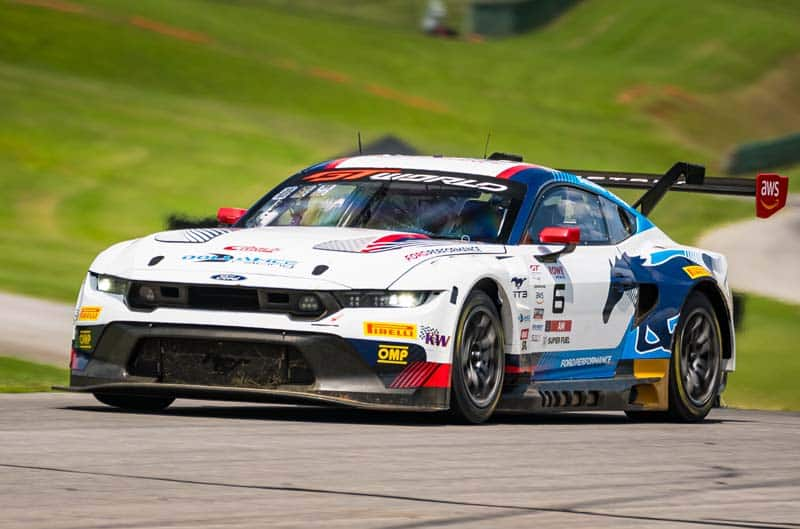
Mustang GT3 Earns Class Victory at VIR
By Ford Performance Staff
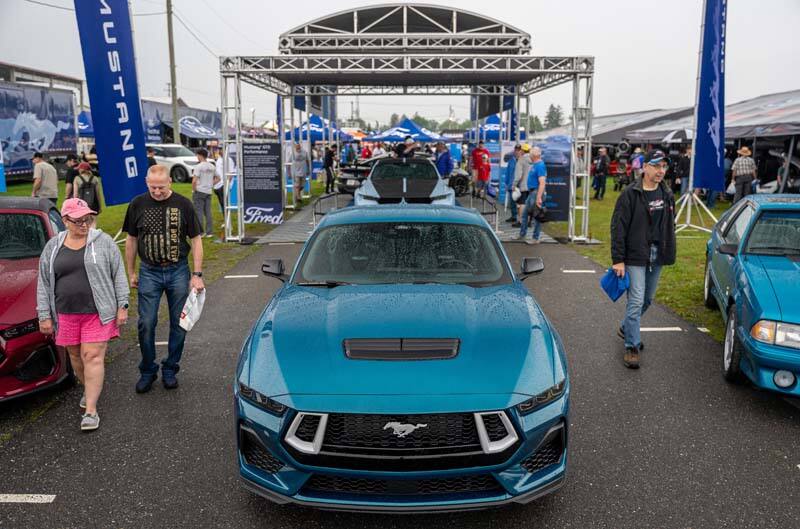
So Here’s What You May Have Missed at the Carlisle Nats
By Joe Deladvitch
{{title}}
{{subTitle}}