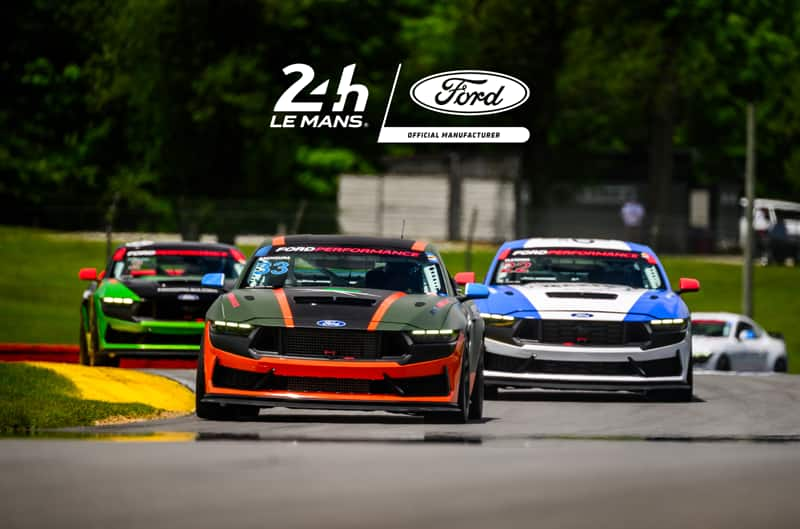
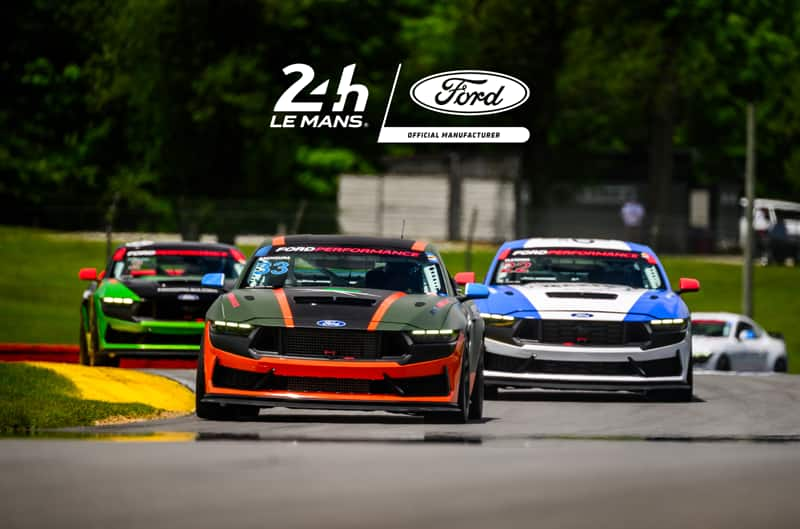
All News
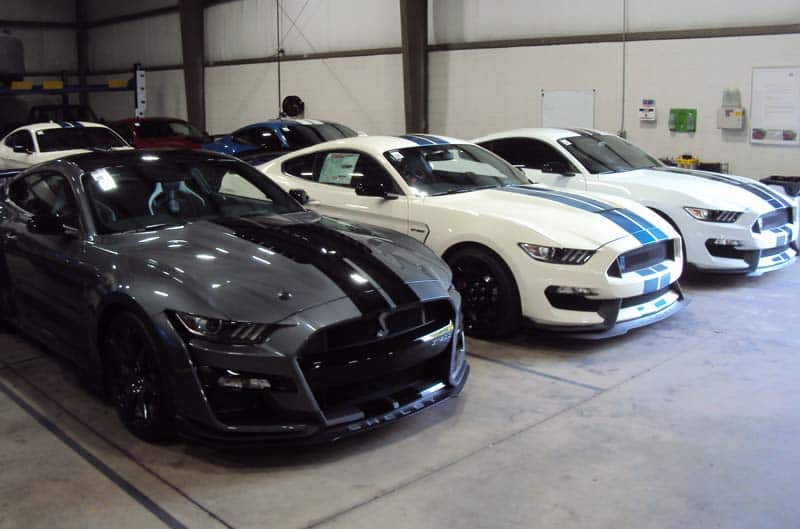
Mustang Featured Car at Northville Concours C&C Event
By John M. Clor
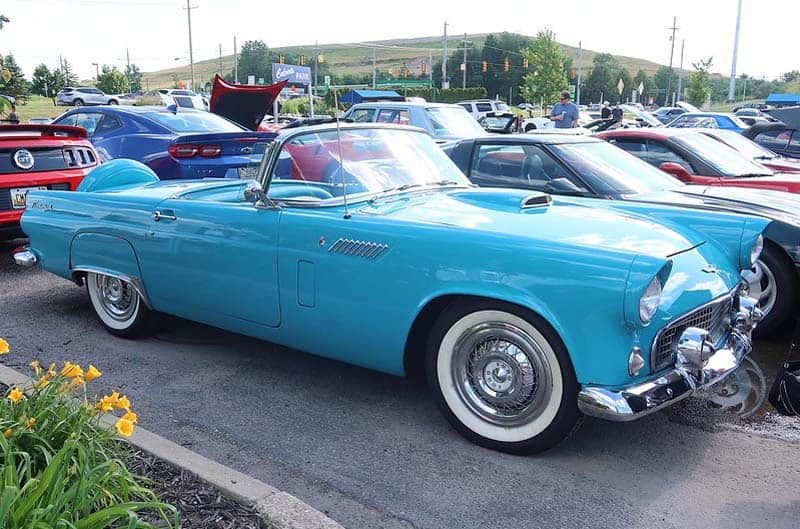
Weekly Fast-Food Cruise-In Serves Up Tasty Fords
By Bill Cook
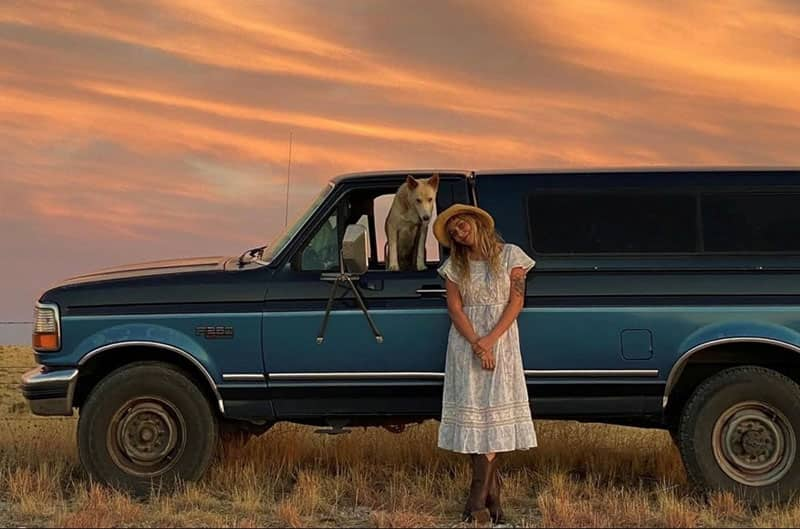
Elle Thompson’s 92 F-250 Builds Bond Beyond Measure
By Elleyna Thompson
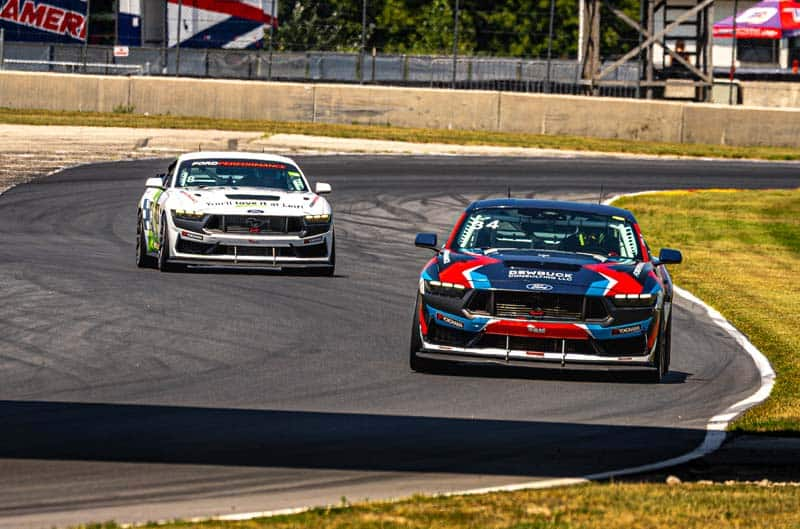
Ford Performance Weekend Highlights | August 10, 2025
By Ford Performance Staff
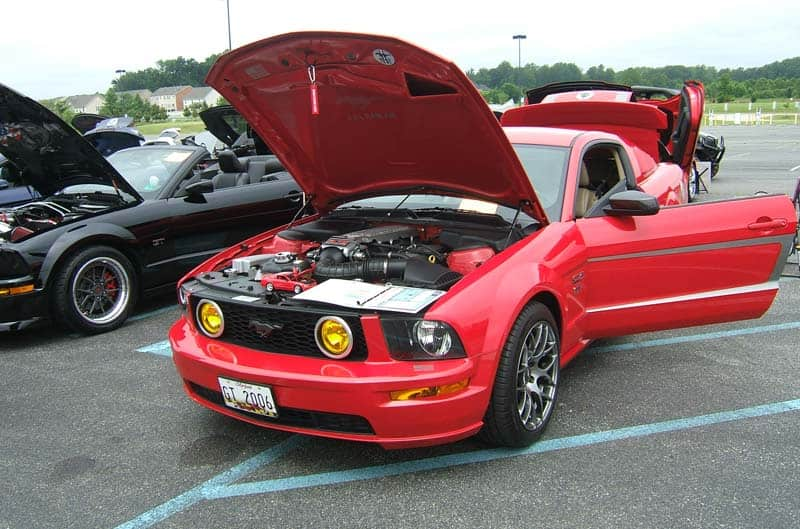
Mustangs Crack Trophy List at the Blue Crabs Show
By Rick Mitchell
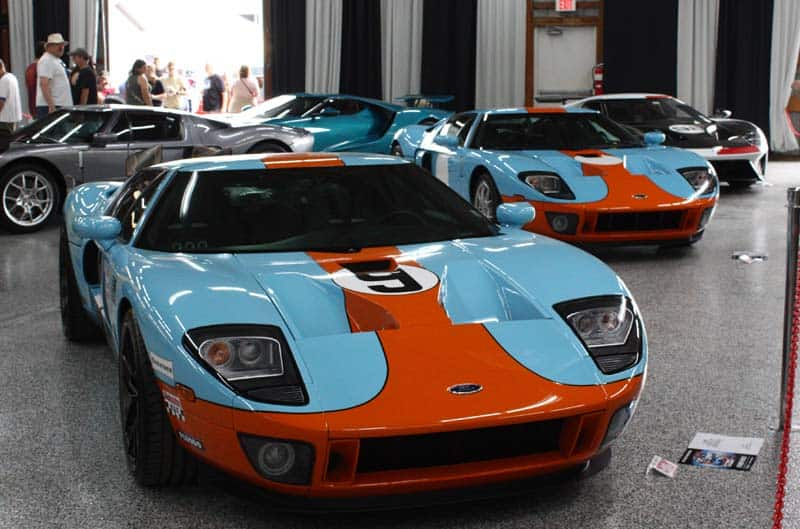
Reunion Celebrates 20th Birthday of the Modern Ford GT
John F. Katz
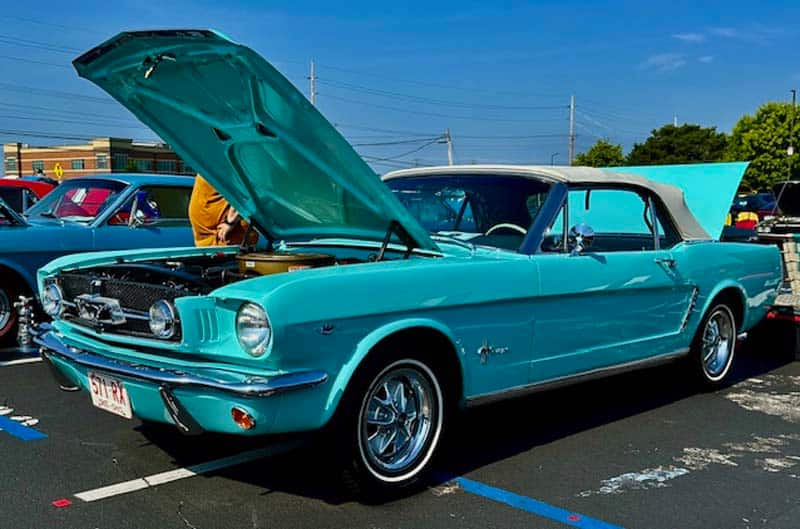
Cool Mustangs Help Fans Beat the Heat at MCA Cincy Nats
By John M. Clor
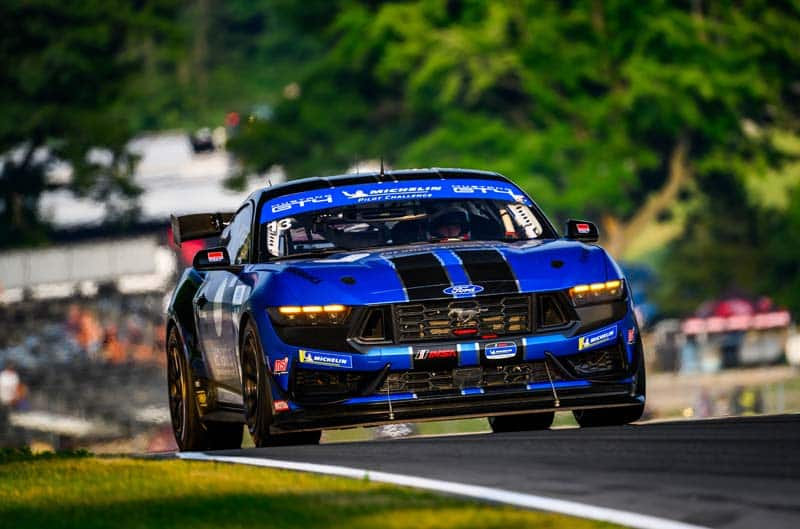
Ford Performance Weekend Highlights | August 3, 2025
By Ford Performance Staff
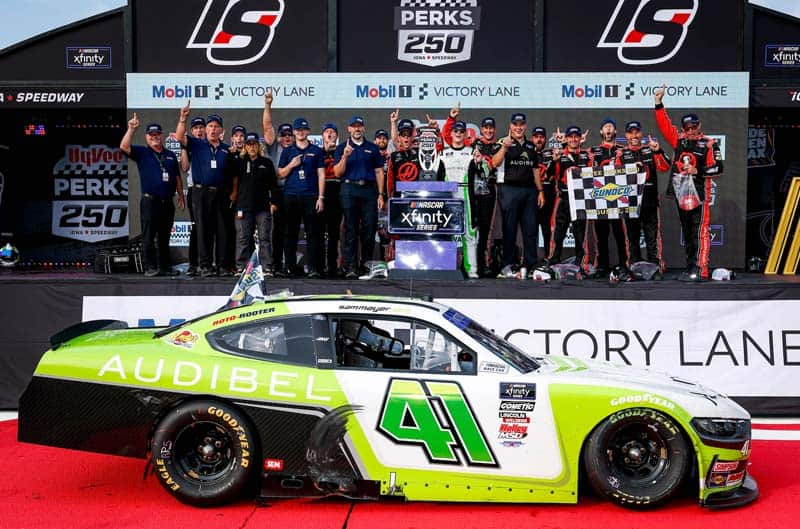
Sam Mayer Scores NASCAR Xfinity Series Win at Iowa
By Ford Performance Staff
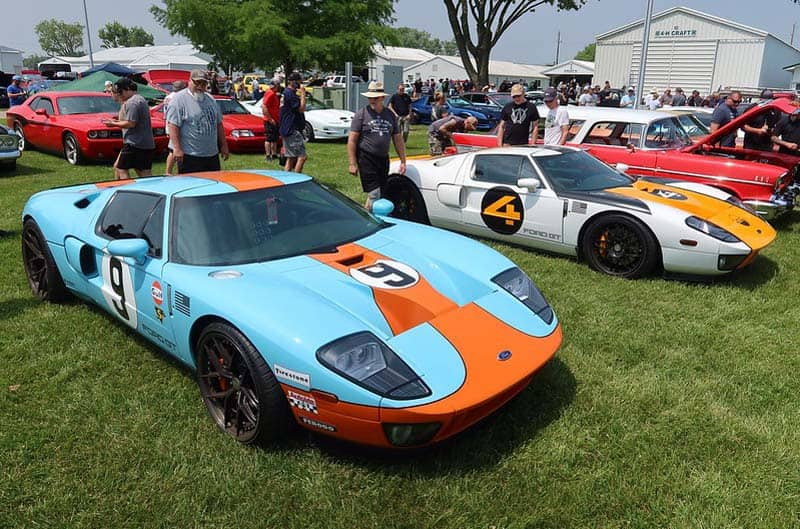
Ford Rides Rev Up Hot Rod Power Tour Stop in Michigan
By Bill Cook

T-Birds Headline Aug. 14 Homecoming Event in Dearborn
By John M. Clor
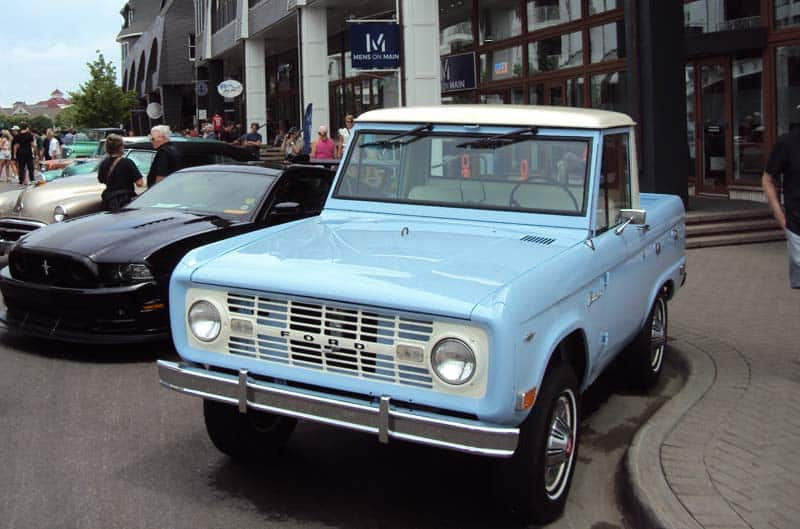
Mustangs Make Waves at Bay Harbor Car & Boat Show
By John M. Clor
{{title}}
{{subTitle}}